By Girish Linganna
Mar 30: On February 21, a space capsule measuring one meter across touched down in the Utah desert following an eight-month orbital mission. Inside, it carried a supply of Ritonavir, an antiviral medication used for HIV and COVID-19 treatment.
The Utah desert, located in the western United States, spans across the state of Utah.
The mission, conducted by the California-based startup Varda Space Industries, was designed to showcase the capability for automated pharmaceutical drug production in space. This endeavor could potentially lead to innovative and more efficient approaches to medicine development, as reported by the BBC media house.
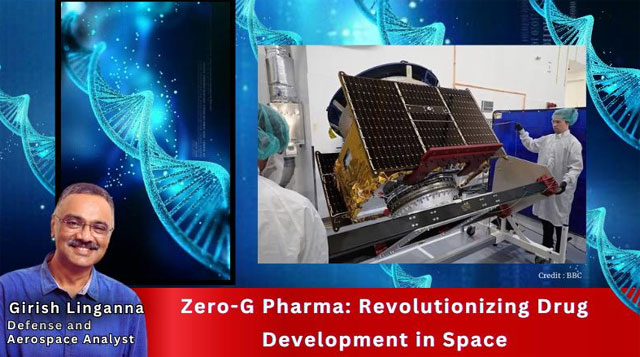
Varda's W-1 mission took off on a SpaceX Falcon 9 rocket in June 2023. The Space capsule, weighing approximately 90kg, has the theoretical capacity to produce almost 100kg of products during its several months in orbit.
However, for this first mission, only a limited quantity of Ritonavir was produced during a test run that lasted 27 hours.
Analysis conducted during the flight suggested that the manufacturing procedure unfolded as expected. Although final outcomes are still pending, Varda is actively gearing up for a second mission, which will transport their inaugural commercial payload.
Why undertake such an endeavor?: Research conducted on the International Space Station and various spacecraft over recent years has demonstrated the feasibility of producing small amounts of pharmaceutical drugs in space.
The reason behind this is that microgravity conditions in space affect the way complex crystalline molecules, like the proteins and antibodies found in various medications for diseases ranging from cancer to heart disease, are formed. These molecules behave differently in space compared to Earth, impacting their development process.
For example, in space, the liquid solutions that crystals grow from don't separate based on density, and solids neither sink nor float within these solutions. Additionally, the absence of gravity ensures that growing structures remain unaltered in shape, preventing any distortion that could change their characteristics.
According to Prof Anne Wilson, a researcher at Butler University in Indianapolis, there's strong evidence that crystals cultivated in a microgravity environment are at least 80% more likely to be of higher quality than those grown on Earth. Prof Wilson, who conducted various experiments in 2022, shared this insight with the BBC, highlighting the advantages of space-based crystal growth.
The professor mentioned that our investigations reveal crystals cultivated in the absence of gravity tend to be more uniform, exhibit enhanced structural integrity, and are often bigger.
Pharmaceutical firms have utilized insights gained from space experiments to refine their manufacturing techniques on Earth. However, crystals produced in space can exhibit unique and beneficial traits, potentially making them more effective than medicines produced on Earth.
Dr. Katie King, a microgravity researcher at the UK-based space medicine company BioOrbit, explained to the BBC, "Microgravity improves crystallization, resulting in crystals that are more flawless and uniform."
This technology enables the creation of exceptionally clear and pure protein crystals, akin to those found in the human body and targeted by medications. By generating these crystals under the zero-gravity conditions of space, we can transport them back to Earth for in-depth analysis. This process provides a clearer understanding of how medicines interact with these proteins. Additionally, the high purity of these space-grown crystals has the potential to enhance the effectiveness of pharmaceuticals.
Varda is exploring the use of microgravity to discover potentially new and more efficacious drug forms. Meanwhile, BioOrbit a pharmaceutical company is focusing on transforming existing medications into forms that patients can easily use at home, according to the BBC.
The cost of manufacturing materials in space for Earth's use poses a significant economic challenge. Although reusable launch vehicles like the Falcon 9 have greatly reduced the cost of reaching orbit, Varda aims to enhance the versatility and reusability of their spacecraft. This strategy involves designing them for easy refurbishment and quick preparation for subsequent launches, aiming for shorter intervals between missions.
Delian Asparouhov, co-founder of the company, mentioned that the initial mission's cost was approximately $12 million (£9.5 million), but he anticipates this could quickly drop to around $2 million (£1.6 million) per mission. The company is already planning to develop larger and more cost-effective space laboratories in future generations, which may encourage other companies to enter the space manufacturing sector.
King highlights the significant advantages, noting that the full potential remains largely unexplored, with much more to discover in the realms of drugs, medicine, and life sciences overall. The innovative aspect of Varda's work lies in their re-entry system, which sets a precedent for other companies to leverage microgravity for diverse new applications.
(The author Girish Linganna of this article is a Defence, Aerospace & Political Analyst based in Bengaluru. He is also Director of ADD Engineering Components, India, Pvt. Ltd, a subsidiary of ADD Engineering GmbH, Germany. You can reach out to him at: girishlinganna@gmail.com)