By Girish Linganna
Mar 21: Agnikul Cosmos is a space start-up based in Chennai, incubated by IIT Madras.
Agnikul Cosmos, is preparing for a test flight of its Agnibaan SOrTeD (Suborbital Tech Demonstrator) rocket on March 22.Agnibaan is a Sanskrit Word ,that translates to mean an "Arrow of Fire".
This launch will highlight India's expanding skills in the private space industry. The rocket, with a unique one-piece 3D printed design and using liquid oxygen and kerosene (stored at room temperature), will be the first of its kind to fly from India's first launchpad built by a private company.
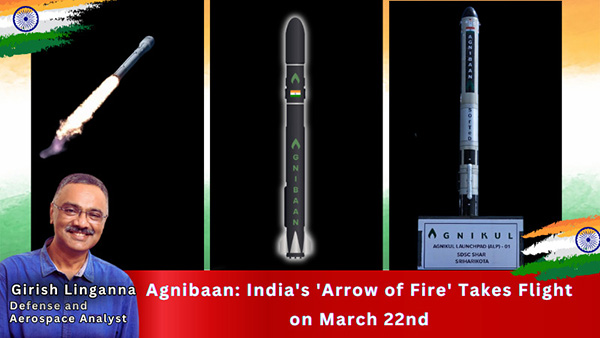
Agnibaan SOrTeD is a sub-orbital tech demonstrator set to test a one-stage rocket powered by "Agnite", a 3D printed semi-cryogenic engine. This engine runs on widely used aviation turbine fuel, or kerosene, and high-purity medical grade liquid oxygen.
This is the nation's first rocket powered by a semi-cryogenic engine and also the first engine that is both designed and made locally in a single 3D printed piece.
Agnikul Cosmos has created Agnibaan, a three-stage rocket that stands 18 meters tall and has a diameter of 1.3 meters. It can transport payloads weighing up to 100kg to a low earth orbit of 700km.
The first stage uses seven Agnite engines. Each engine provides 25 kN of thrust when at sea level.The second stage of the rocket is powered by the same Agnite engine. Additionally, there's an optional smaller third stage, enclosed within the rocket's nose cone, designed to carry one or multiple tiny satellites.
The rocket's engines are run by fuel pumps that batteries and electric motors power. For safe moving and shipping, the rocket doesn't use any explosives or firework-like materials. Instead, it uses air pressure systems to separate the rocket's stages.
The entire combustion section of the rocket is a one-piece unit made through 3D printing. Important components of Agnibaan, such as the engines, pumps, motor and package casings, are all 3D printed at the Agnikul Rocket Factory.
ThIs Rocket facility is capable of manufacturing two rocket engines per week, potentially allowing for the assembly of one launch vehicle each month.
The company wants to serve the expanding market for launching small satellites and presents Agnibaan as a versatile rocket for sending small satellites into low earth orbit.
First Flight Information
The first flight of Agnibaan will be a sub-orbital one, meaning the rocket won't go into space.It will be a controlled, straight-up flight. Once it hits 10 km high, the rocket will start coming down and land in the Bay of Bengal, roughly 30 km away from its launch point.
Objectives of Test Launch
The test flight of Agnibaan will include all the navigation, communication, and direction systems typically used in the rocket's commercial launches.The main goal of the test flight is to check the company's technology and confirm how well the different parts and smaller systems of the vehicle work.
Private Launch Site and Mission Control Center
In November 2022, Agnikul opened India's first private rocket launch site and mission control center, located at the ISRO spaceport in Sriharikota.The company is developing a technique to launch rockets from a platform mounted on the back of a truck, making it more adaptable and movable than conventional launch methods.
Definitions
i) A 3D printed engine is an engine created by fabricating its parts layer by layer using 3D printing technology. This manufacturing method offers increased design flexibility, faster production, and potential cost savings. It allows for highly intricate and customized engine components, optimizing performance and efficiency in various applications.
ii) A semi-cryogenic engine uses a mixture of liquid oxygen and kerosene (maintained at room temperature)as propellants, while a cryogenic engine employs liquid hydrogen and liquid oxygen (both maintained at sub-zero temperatures) . The main difference lies in the type of fuel used. Cryogenic engines offer higher specific impulse and greater efficiency due to the higher energy content of liquid hydrogen. They are suitable for heavier payloads. Semi-cryogenic engines have a simpler design and lower operational costs, making them advantageous for smaller payloads and cost-sensitive missions.
(The author Girish Linganna of this article is a Defence, Aerospace & Political Analyst based in Bengaluru. He is also Director of ADD Engineering Components, India, Pvt. Ltd, a subsidiary of ADD Engineering GmbH, Germany. You can reach out to him at: girishlinganna@gmail.com)